High-Quality 4-Axis CNC Machining Services: Precision, Flexibility, and Cost Efficiency
In today’s competitive manufacturing landscape, precision and efficiency are paramount. High-quality 4-Axis CNC Machining Services offer an ideal balance between complex part processing and cost-effective production. By leveraging advanced multi-axis systems, manufacturers can achieve superior accuracy, streamlined workflows, and rapid turnaround times—all critical for industries such as automotive, aerospace, and medical.
1. What is 4-Axis CNC Machining?
Four-axis CNC machining enhances traditional three-axis systems by incorporating a rotary axis (commonly labeled A or B), enabling multi-angle cutting and machining. This extra axis allows for:
- Single Clamping Efficiency: Minimizes repeated clamping errors, ensuring a tolerance as fine as ±0.02 mm.
- Cost-Effectiveness: Typically, these systems reduce expenses by around 30% compared to five-axis machines, making them ideal for small to medium batch production.
- Material Versatility: Capable of handling a broad range of materials—including metals like aluminum, steel, titanium; plastics such as ABS and nylon; and various composite materials.
This technology is essential for precision parts such as cylinders, bevels, and spiral grooves, where traditional machining might struggle with consistency and accuracy.
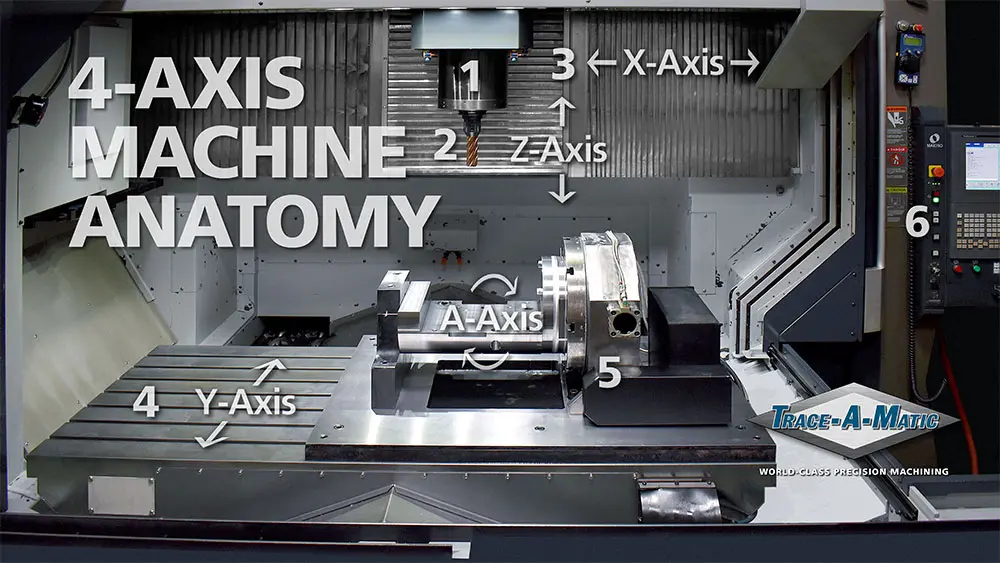
2. Key Applications of 4-Axis CNC Machining
High-quality 4-Axis CNC Machining Services are used across multiple industries due to their versatility and precision. Below is an overview of typical applications:
- Automobile Manufacturing:
- Parts: Camshafts and transmission gears.
- Processes: Multi-angle milling and spiral groove processing.
- Materials: Alloy steel and aluminum alloy.
- Aerospace:
- Parts: Hydraulic joints and brackets.
- Processes: Circular drilling and bevel milling.
- Materials: Titanium alloy and stainless steel.
- Medical Equipment:
- Parts: Surgical instrument handles and implant bases.
- Processes: Precision turning and micron-level engraving.
- Materials: Stainless steel 316L and PEEK.
- Industrial Machinery:
- Parts: Pump bodies and valve housings.
- Processes: Deep hole drilling and surface contour processing.
- Materials: Cast iron and brass.
By targeting these sectors, CNC machining services expand their reach using long-tail keywords such as “precision CNC machining for automotive components” and “advanced 4-axis machining for aerospace applications.”
3. Why Choose 4-Axis Over 3-Axis or 5-Axis?
When evaluating CNC machining solutions, it’s essential to compare the capabilities:
- Compared to 3-Axis Machining:
- Efficiency: The additional rotary axis reduces clamping times and enables cylindrical processing (ideal for gear shafts), leading to up to a 40% boost in efficiency.
- Precision: Enhanced machining angles allow for superior surface finishes and dimensional accuracy.
- Compared to 5-Axis Machining:
- Cost Savings: Lower equipment costs make 4-axis systems more budget-friendly, particularly for fixed-angle processes that do not require the dynamic linkage of five-axis systems.
- Optimal for Medium Complexity: They are best suited for medium-complexity parts, such as shaft components with spiral grooves, meeting both quality and cost efficiency.
This comparative advantage positions 4-Axis CNC Machining as the ideal choice for customers seeking a balance between performance and investment.
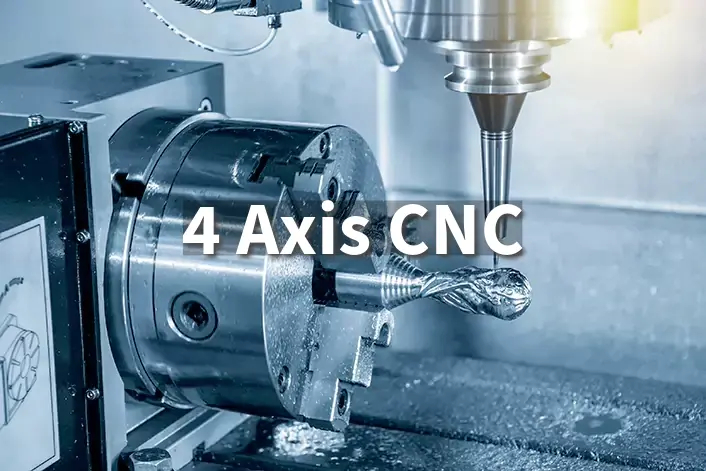
4. Technical Capabilities of High-Quality 4-Axis Services
State-of-the-art 4-axis machining centers integrate advanced features designed to meet the most stringent production demands:
- Advanced Equipment:
- Machines like the Haas UMC-750 or Mazak VTC series offer high precision and support workpiece sizes up to Ø500 mm × 300 mm.
- Automation and Robotics:
- Robot-assisted clamping systems enable 24/7 continuous production, ensuring consistent quality and reduced manual intervention.
- Post-Processing Technologies:
- Surface Treatments: Options include anodizing for corrosion resistance, sandblasting for a controlled surface roughness (Ra 0.8–1.6 μm), and electroplating for enhanced wear resistance.
- Function Enhancements: Heat treatments (quenching, annealing) and laser marking provide both functional improvements and permanent identification.
- Quality Assurance:
- Use of three-dimensional measuring instruments (CMM) and spectrum analyzers ensures parts meet exacting standards, backed by certifications like ISO 9001, IATF 16949 (automotive), and ISO 13485 (medical).
These technical capabilities underscore the value of high-quality 4-Axis CNC Machining Services for industries demanding precision and repeatability.
5. Case Study: Automotive Camshaft Production
An automotive manufacturer required 1,000 alloy steel camshafts with spiral oil grooves and precise end holes, originally quoted at $85 per piece with an uncertain delivery timeline of six weeks by a local supplier.
Challenge:
The local option was too costly and risked delays, jeopardizing production schedules.
Solution:
By opting for Great Light’s advanced 4-Axis CNC Machining Services, the manufacturer benefited from:
- Optimized Tool Path and Cooling Solutions: Resulting in enhanced machining efficiency.
- Cost Reduction: The final cost was lowered to $35 per piece.
- Faster Delivery: Production turnaround was shortened to three weeks.
- Quality Assurance: Achieving a defect rate of less than 0.5%.
This case study exemplifies how precision 4-axis machining can transform production economics while maintaining superior quality.
6. How to Select a 4-Axis CNC Supplier
Choosing the right supplier is critical to ensure seamless manufacturing outcomes. Key evaluation criteria include:
- Equipment Capabilities:
- Verify that the supplier’s equipment is modern, with features like a high-rigidity rotary table (e.g., a Nikken 4-axis rotary table) to handle complex geometries.
- Industry Experience:
- Look for certifications relevant to your industry (for example, IATF 16949 for automotive or ISO 13485 for medical).
- Digital Services and Transparency:
- Suppliers offering online quotations and real-time production tracking (such as integrated order management systems) ensure transparency and speed.
- Supplier Comparison:
- Online Providers: Often offer transparent pricing (30–50% lower), global material sourcing, and rapid delivery (within 5–7 days).
- Local Suppliers: Can provide an edge in urgent order response, typically within 24–48 hours.
By carefully evaluating these factors, businesses can secure a CNC machining partner that aligns with their quality and delivery expectations.
7. Future Trends in 4-Axis Machining
The evolution of CNC machining technology is driving the industry toward smarter, greener, and more integrated solutions:
- Intelligent Upgrades:
- Integration of IoT sensors to monitor tool wear in real time can reduce machine downtime by approximately 20%.
- Hybrid Manufacturing:
- Combining four-axis CNC machining with 3D printing opens new avenues for producing conformal cooling molds and complex geometries.
- Green Technology:
- Adoption of micro-lubrication (MQL) technology helps minimize cutting fluid pollution, aligning manufacturing processes with sustainable practices.
These trends ensure that High-Quality 4-Axis CNC Machining Services continue to evolve, offering enhanced performance, environmental benefits, and innovative manufacturing solutions.
8. Why Choose Great Light?
Great Light stands out in the competitive CNC machining market for several compelling reasons:
- Extensive Equipment Scale:
- With over 30 four-axis CNC machines available, Great Light can accommodate workpieces up to Ø600 mm × 400 mm, ensuring versatility in handling complex parts.
- Rapid Turnaround:
- Standard production cycles range from 5–7 days, with expedited services delivering in as little as 72 hours.
- Competitive Pricing:
- Tiered discount structures for bulk orders and a 10% discount on first orders make high-quality machining accessible.
- Comprehensive One-Stop Service:
- From design optimization (DFM analysis) to full post-processing (including packaging logistics), Great Light covers every step in the production process.
- Material Expertise:
- The service supports over 30 metals and engineering plastics, including special alloys like titanium alloy Ti6Al4V.
- Digital Integration:
- Customers can upload design files for real-time quotes and benefit from free DFM suggestions, making the entire process streamlined and transparent.
These core advantages make Great Light a trusted partner for precision 4-Axis CNC Machining Services worldwide.
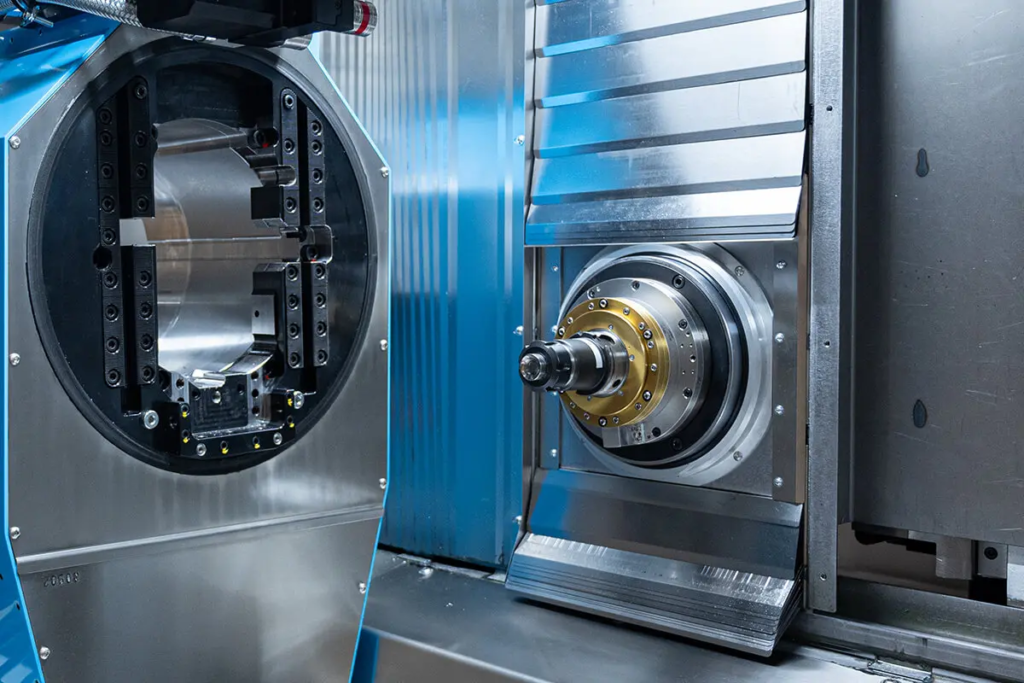
9. Conclusion
High-quality 4-Axis CNC Machining Services represent a powerful solution that balances complexity with cost efficiency. They are particularly suited for industries such as automotive, aerospace, and medical where precision and reliability are non-negotiable. With advanced machinery, state-of-the-art automation, and a robust digital infrastructure, providers like Great Light deliver unparalleled precision manufacturing solutions. By choosing a partner that meets strict industry standards and embraces innovation, businesses can confidently customize their parts, improve turnaround times, and achieve long-term cost savings. Embrace the future of efficient production—customize your precision complex parts now and experience the next generation of CNC Machining Services.